Part Shapes
2D Shapes
A 2-dimensional shape can be defined as a flat surface contained within a closed boundary.
A 2D shape has length and width, but no height. While real-world parts are defined as 3D
shapes, an understanding of 2D shapes is equally important. When designing a part, 2D shapes
are used as part surfaces, cross-sectional surfaces, and projected surfaces. These concepts
will be explored later in the lesson.
One type of 2D shape is that formed by a curved boundary, such as the following:
2D shapes formed by a boundary of straight lines are called polygons and can
have any number of sides.
Triangle |
Quadrilateral |
Octagon |
If all sides are of equal length and separated by equal angles, the shape is
called a regular polygon.
Regular hexagon |
Irregular hexagon |
If all interior angles of the polygon are less than 180 degrees, it is defined as
convex. Otherwise, the polygon is concave. All regular polygons are convex.
Convex polygon |
Concave polygon |
3D Shapes
A 3-dimensional shape is a solid object which is bound by several connected
surfaces. A 3D shape has length, width, and height. The surfaces of some simple
3D shapes are all polygons, as shown below.
Other basic 3D shapes include curved surfaces.
Part Shapes
The 3D shapes of real-world parts typically do not resemble the simple shapes previously
shown. They are often highly complex and include numerous contoured surfaces and features.
However, any 3D shape can be classified as some basic shape that it most closely remsembles.
This is useful for identifying a compatible manufacturing process that is best suited for a
given 3D shape. One method of classifying parts is using the following 7 categories:
- Flat - Most suitable for sheetmetal forming, but flat plastic parts can be molded.
Basic shape |
Example: Sheetmetal vent |
Example: Molded lid |
- Thin-walled: Cylindrical - Metal parts typically machined using turning, while
plastic parts are molded. For some simple parts (metal or plastic), extrusion can be used.
Basic shape |
Example: Turned part |
Example: Molded cover |
- Thin-walled: Cubic - Metal parts typically machined using milling or formed
from sheetmetal, while plastic parts are molded. For some simple parts (metal or plastic),
extrusion can be used.
Basic shape |
Example: Molded box |
Example: Sheetmetal bracket |
- Thin-walled: Complex - Complex parts are typically formed using molding/casting
processes, but can also be formed from sheetmetal.
Basic shape |
Example: Molded housing |
Example: Sheetmetal support |
- Solid: Cylindrical - Metal parts typically machined using turning or formed
using casting. Solid plastic parts can be molded if they are small. For some simple parts (metal
or plastic), extrusion can be used.
Basic shape |
Example: Turned part |
Example: Cast pulley |
- Solid: Cubic - Metal parts typically machined using milling or formed using
casting. Solid plastic parts can be molded if they are small. For some simple parts (metal
or plastic), extrusion can be used.
Basic shape |
Example: Milled toolholder |
Example: Cast handle |
- Solid: Complex - Complex parts are typically formed using casting,
forging, or machining. Solid plastic parts can be molded if they are small.
processes
Basic shape |
Example: Cast pedal |
Example: Milled part |
Aspect ratio
The aspect ratio of a part is another way to characterize the part's shape. The
aspect ratio can be measured in different ways, but typically describes the ratio
of the part's height to its width. Therefore, a part with a high aspect ratio is
tall and thin, while a part with a low aspect ratio is short and wide.
For cylindrical parts, the aspect ratio can be calculated as the height divided
by the diameter.
High aspect ratio part |
Low aspect ratio part |
For cubic, or more complex parts, the aspect ratio is often calculated as the height
divided by the diagonal between the length and width. The diagonal is used because it
accounts for both the length and width of the part.
High aspect ratio part |
Low aspect ratio part |
Cross section
Identifying the cross sections of a part are useful in both the
design and manufacture of many parts. A cross section is the
surface that results from slicing a part by a plane. For most
parts, the cross section will be different depending on the
location and orientation of the slice. However, some simple
parts have a uniform cross-section along one or more axes.
Uniform cross section |
Non-uniform cross section |
Part Features
Features
Most parts have a main solid body with numerous features that modify its shape.
These features can usually be classified as depressions in the part or protrusions
from the surface. There are also angles or curves that can be applied to the part.
The types of features on a part often dictate which manufacturing processes can be
used to form the part. However, sometimes one process will be used to form
the main body of the part and additional operations will be used form the more
complex features. When a feature is not formed by the primary process, it is
typically referred to as a secondary feature.
Cast housing with highlighted features
Depressions: Pockets
A pocket is a depression that does meet the criteria to be considered a hole or a slot.
If a feature has a uniform cross section along its depth, but has a low aspect ratio
it is considered a pocket, not a hole. Also, a feature with a high aspect ratio but a
non-uniform cross-section is also a pocket, not a hole.
Low aspect ratio pocket, not a hole |
Non-uniform pocket, not a hole |
A feature with a uniform cross section along its length that is not very long is
considered a pocket, not a slot. Also, a feature that is sufficiently long but has a
non-uniform cross-section along its length is considered a pocket, not a slot.
Wide pocket, not a slot |
Non-uniform pocket, not a slot |
As seen in the above examples, a pocket can have a uniform or non-uniform cross section
along any direction. As with holes and slots, the cross-section of a pocket can be a
regular polygon, or any irregular shape. Also, a pocket does not necessarily require a
flat base. In fact, a pocket will typically have a contoured base. When a pocket combines
many of the elements described above, such as an irregular and non-uniform cross-section
and a contoured base, it can take on a highly complex form.
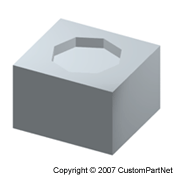
Regular cross section |
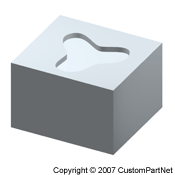
Irregular cross section |
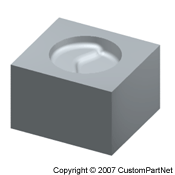
Contoured base |
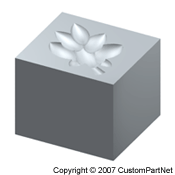
Highly complex pocket |
Lastly, much like a slot, a pocket can be located on the part in a variety of ways. Most
pockets, like those shown above, are contained within the main body of the part. However,
a pocket can also extend to one or several surfaces of a part.
2 types of partial pockets |
Through pocket |
Depressions: Captured cavities
A captured cavity is a pocket with inward curving surfaces, often called reentrant surfaces.
If a solid object were to fill such a cavity, it could not be removed. Many manufacturing
processes are incapable of producing parts with such a feature. A variation on a captured
cavity is an enclosed cavity, in which the pocket is surrounded on all sides by surfaces
of the part. There are very few manufacturing processes that can form an enclosed cavity
in a part. The easiest way to form an enclosed cavity is by joining two or more parts together.
Captured cavity |
Enclosed cavity |
Protrusions: Bosses
A boss is a protrusion on a part with a high aspect ratio. In a sense, it is the inverse of
a hole, but does not necessarily require a uniform cross-section. Most bosses have a circular
cross-section and form a cylindrical boss. However, a boss can have a polygonal, irregular,
or any non-uniform cross-section.
Cylindrical boss |
Square boss |
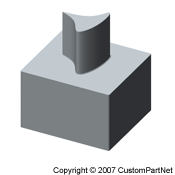
Irregular boss |
Non-uniform boss |
Bosses are often times designed with a hole in the center, forming a hollow boss. Much like
the boss itself, the hole can have a variety of shapes. Another type of boss, is a threaded
boss, which can be a cylindrical boss with external threads or any boss with a threaded
cylindrical hole.
Hollow boss |
Hollow boss |
Threaded boss |
Threaded boss |
Bosses can occur along any axis, but for ease of manufacture, are typically oriented
vertically or horizontally. However, angled bosses are sometimes used.
Protrusions: Gussets
A gusset is a triangularly shaped protrusion that connects two surfaces to offer additional
support. A gusset is typically used between a wall of a part and the flat surface from which it
protrudes. Gussets are also used to support other features, such as bosses, ribs, and steps.
Wall gussets |
Boss gussets |
Multi-axis features
All of the above features (holes, slots, pockets, bosses, ribs, steps, etc.) can occur along any axis.
Typically, all features on a part occur along the same axis because it will be easier to manufacture.
Whether the features are made by a mold, machining tool, sheetmetal blank, or other device, a single axis
means the tool will always move in the same direction, referred to as the tooling direction. Multi-axis
features require additional tooling directions which will add time and cost to the manufacture of the part.
In molding and casting processes, features that are not along the tooling direction are referred to as
undercuts and can occur externally or internally.
Uni-axial features |
Multi-axis features |